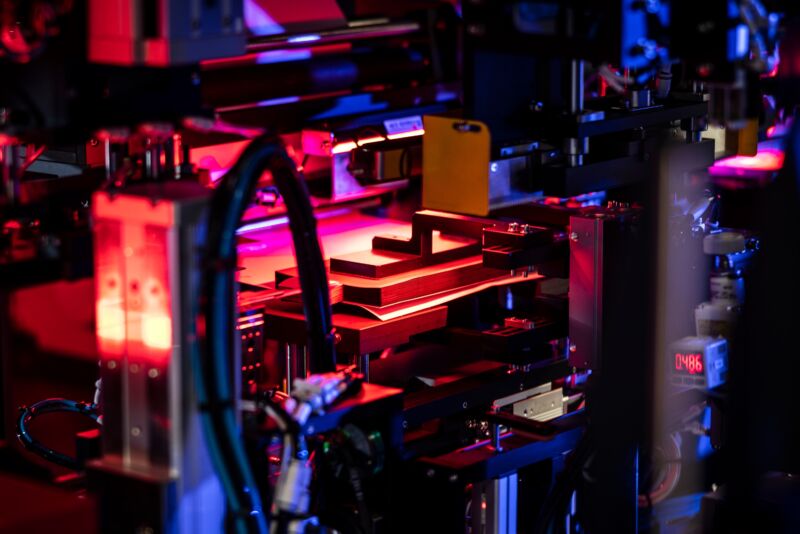
Solid Power, a Colorado-based battery developer, moved one step closer to producing solid-state batteries for electric vehicles on Monday. The company has completed an automated “EV cell pilot line” with a capacity to make approximately 15,000 cells per year, which will be used for testing first by Solid Power and then by its OEM partners.
“The installation of this EV cell pilot line will allow us to produce EV-scale cells suitable to start the formal vehicle qualification process. In the coming quarters, we will work to get the EV cell pilot line fully operational. and look forward to delivering full EV-scale solid-state cells to our partners later this year,” said Doug Campbell, CEO of Solid Power.
Solid state batteries differ from the lithium-ion batteries currently used in EVs in that they replace the liquid electrolyte with a solid layer between the anode and cathode. It’s an attractive technology for several reasons: Solid-state cells should have a higher energy density, they should be able to charge faster and they should be safer because they are non-flammable (which should further reduce pack density and weight , because it needs less robust protection).
It’s one of those technologies that takes forever to a very casual observer, but in Europe there are already operational Mercedes-Benz eCitaro buses with solid-state packs.
It will take a little longer for the technology to be ready for passenger electric vehicles, but it seems to be maturing. Solid Power is one of the leading developers of solid-state batteries, founded in 2012. Its approach is to use a sulfur-based solid electrolyte and an anode with a very high silicon content — more than 50 percent, according to Solid Power.
Ars alumnus Tim de Chant described the production process in a 2021 article for The Wire China:
Aside from the Rocky Mountain backdrop in the distance, Solid Power’s low-slung factory looks like any other battery factory. Inside, barrels of chemicals are mixed into a slurry and coated on thin metal plates. The chemicals are pressed to the surface through a series of rollers resembling a miniature printing press, and towards the end of the line the prepared sheets are cut, stacked and pressed into a bag-like housing.
At this point, other manufacturers would inject the pouch with a liquid known as an electrolyte, which allows ions to move across the battery during use. But thanks to Solid Power’s innovation, it can simply close the case and move on to the next one.
This new line is designed to produce the same large format pouch cells currently used by automotive OEMs in their EVs, with cell capacities ranging from 60-100 Ah. BMW and Ford will be the first automakers to receive cells for testing by the end of this year.