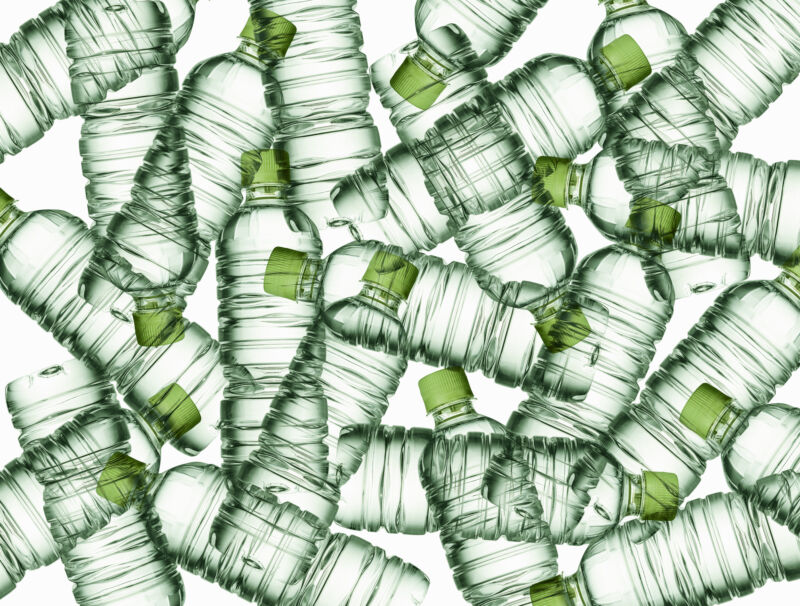
Yagi Studio | Getty Images
Since the first factories began producing polyester from petroleum in the 1950s, humans have produced an estimated 9.1 billion tons of plastic. Less than a tenth of the waste created from that plastic is recycled, researchers estimate. About 12 percent were burned, releasing dioxins and other carcinogens into the air. Most of the rest, a mass equivalent to about 35 million blue whales, has accumulated in landfills and in the natural environment. Plastic lives in the oceans and accumulates in the guts of gulls and great white sharks. It is raining, in small patches, on cities and national parks. According to some studies, it is responsible for more greenhouse gas emissions than the aviation industry from production to disposal.
This pollution problem is exacerbated, experts say, by the fact that even the small amount of plastic that does get recycled ends up in landfills sooner or later. Conventional thermomechanical recycling – where old containers are flaked, washed, melted and then transformed into new products – inevitably produces products that are more brittle and less durable than the starting material. At best, material from a plastic bottle can be recycled about three times in this way before it becomes unusable. It is more likely to be ‘downcycled’ into lower value materials such as clothing and carpeting – materials that will eventually end up in landfills.
“Thermomechanical recycling is not recycling,” said Alain Marty, chief science officer at Carbios, a French company developing alternatives to conventional recycling.
“Eventually,” he added, “you’ll have exactly the same amount of plastic waste.”
Carbios is among a contingent of startups trying to commercialize a type of chemical recycling known as depolymerization, which breaks down polymers — the chain-like molecules that make up a plastic — into their fundamental molecular building blocks called monomers. Those monomers can then be reassembled into polymers that are as good as new in terms of physical properties. In theory, proponents say, a single plastic bottle could be recycled this way until the end of time.
But some experts warn that depolymerization and other forms of chemical recycling could face many of the same problems that already plague the recycling industry, including competition from cheap new plastics made from petroleum feedstocks. They say that to stem the tide of plastic landfills and the oceans, what is most needed is not new recycling technologies, but stricter regulations for plastic producers – and stronger incentives to use the recycling technologies that already exist.
However, buoyed by potentially lucrative business partnerships and tightening European restrictions on plastic producers, Carbios is pursuing its vision of a circular plastic economy – one that does not require the extraction of petroleum to make new plastics. The company’s approach is based on a technology that remains unconventional in recycling: genetically modified enzymes.
Ecatalyze enzymes chemical reactions in organisms. In the human body, for example, enzymes can convert starch into sugars and proteins into amino acids. In recent years, Carbios has refined a method that uses an enzyme found in a microorganism to convert polyethylene terephthalate (PET), a common ingredient in textiles and plastic bottles, into its constituent monomers, terephthalic acid and monoethylene glycol.
Although scientists have known about the existence of plastic-eating enzymes for years — and Marty says Carbios has been working on enzymatic recycling technology since its inception in 2011 — a discovery six years ago outside a bottle recycling plant in Sakai, Japan, helped to energize the field. There, a group led by researchers from Kyoto Institute of Technology and Keio University found a single bacterial species, Ideonella sakaiensis, which can both break down PET and use it for food. The microbe harbored a pair of enzymes that together could cleave the molecular bonds that hold PET together. In the wake of the discovery, other research groups identified other enzymes that could perform the same feat.